Understanding FIFO Inventory Management Techniques
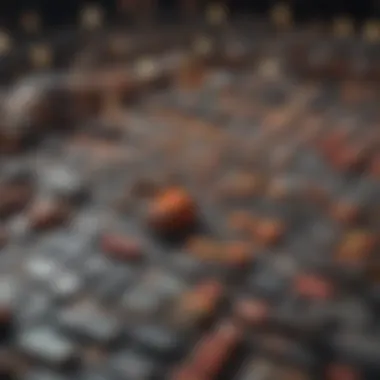
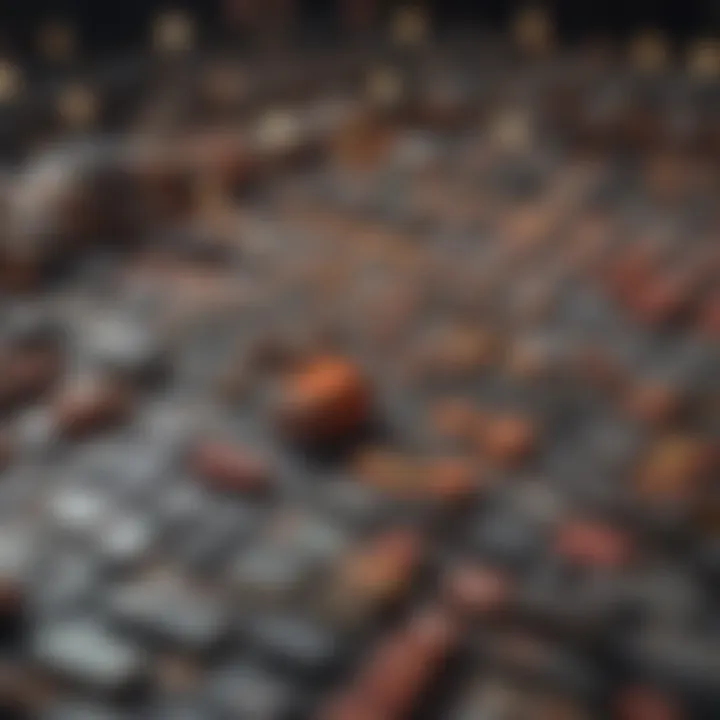
Intro
Navigating the labyrinth of inventory management can often feel like chasing your tail. Among the myriad of strategies available, First In First Out (FIFO) has emerged as a pivotal method, particularly in sectors where the timeliness of product turnover is crucial. In a world that increasingly prioritizes efficiency and clarity, understanding FIFO is akin to possessing a compass in uncharted waters.
But what is FIFO, really? At its core, FIFO is simple: the first items added to inventory are the first ones to be sold or used. This approach not only simplifies the tracking of inventory but also mitigates the risks of spoilage or obsolescenceāespecially in industries such as food services or pharmaceuticals, where timelines are a matter of paramount importance.
For investors and business owners alike, grasping FIFO equips them to optimize their resource management, subsequently enhancing profitability while providing clearer insights into financial health. Whether you're looking to bolster your existing strategies or learning the ropes for the first time, delving into FIFO can empower you to approach inventory management with confidence.
Preface to FIFO Inventory Management
When it comes to managing inventory, especially in industries where products have a limited shelf life, the First In First Out (FIFO) method comes to the forefront. FIFO is not just a process but a lifeline for many businesses that need to keep their stock as fresh and relevant as possible. This section will help to unpack the significance of FIFO in inventory management while shedding light on its core principles and its overarching importance.
Definition and Core Principles
First In First Out, or FIFO, operates on a fundamental principle: the first items placed in inventory should be the first ones sold or used. Imagine stockpiling old newspapers; the ones at the bottom are often those that go unread while the fresher ones on top get all the attention. Simply put, FIFO ensures that older inventory moves out swiftly, preventing stagnation and potential waste.
In practice, FIFO emphasizes the rotation of stock, which can be crucial in sectors like food services, pharmaceuticals, and electronics where obsolescence or spoilage can significantly impact profits. Implementing FIFO requires a keen observation of expiration dates and a consistent workflow to assure that the inventory is not just sorted but also monitored effectively.
The Importance of Inventory Management
Effective inventory management is akin to keeping the heartbeat of a business steady. Poor inventory practices can lead to hefty losses, particularly in sectors reliant on perishable goods. FIFO plays a critical role here because it provides a systematic way to manage products, ensuring that businesses can meet demand without excess waste.
Furthermore, FIFO can influence several internal and external factors that are pivotal to an organizationās success:
- Cost Control: By shifting older stock swiftly, businesses minimize the risk of inventory markdowns, thus preserving profit margins.
- Cash Flow Dynamics: In industries where cash flow is king, efficient turnover of goods can boost liquidity, enabling reinvestment.
- Regulatory Compliance: Certain industries require strict adherence to health and safety standardsāFIFO can help maintain these necessary protocols.
"Keeping inventory fresh is not just good practice; it's essential for survival in many sectors."
As we delve deeper into FIFO through various angles, it's important to remember that good inventory management isn't merely about knowing when to sell; itās about understanding why it matters in the first place.
Historical Context and Development
Understanding the historical context and development of FIFO is crucial in grasping its place in modern inventory management. This section seeks to explore the origins and evolution of FIFO practices, highlighting its significance not just as a mere method but as a foundational principle that underpins effective inventory control.
Origins of FIFO in Inventory Practices
The concept of First In First Out (FIFO) dates back to the days when merchants had to deal with perishable goods. Taking a stroll down memory lane, one can consider the markets of yore, where food items were often sold without any sophisticated preservation methods. The tendency was clear: sell the oldest stock first to minimize spoilage. In those bustling bazaars, merchants learned the hard way that delay could mean throwing away unsold produce.
As time marched on, FIFO became formalized into business practices. In the early 20th century, the rise of warehouse management brought a structured approach to inventory control. The push towards efficiency was palpable, as companies sought out methods that not only improved cash flow but also reduced waste. Indeed, FIFO cemented itself in industries where products had limited shelf lives, such as groceries and pharmaceuticals.
This method wasn't just about keeping things fresh; it also introduced a level of operational discipline that fostered greater accountability. As businesses grew, so did the complexity of their inventories, reinforcing the necessity to adopt systems that could help manage their goods effectively.
Evolution of Inventory Methods
As the landscape of commerce evolved, so did inventory management methods. The mid-20th century, characterized by rapid industrialization and globalization, witnessed a shift in methodologies. Alongside FIFO, methods like LIFO (Last In First Out) emerged. While each method has its own merits, FIFO was favored for sectors dealing with perishable items.
With the emergence of computer systems in the late 20th century, inventory management underwent a further transformation. Traditional techniques had to adapt to digital realities, leading to integrated technologies that facilitated better tracking and forecasting. Whether it was through barcoding or more sophisticated inventory management systems, FIFO became increasingly streamlined and efficient. Companies could now automate their processes, minimizing human error and improving accuracy in stock rotation.
Today, FIFO isn't just a relic of the past; it's a dynamic tool utilized across various industries. From grocery stores that rely on its principles to ensure fresh goods on the shelves, to pharmaceuticals that must adhere to strict regulatory standards regarding the selling of medications, FIFO remains integral.
"Implementing FIFO effectively requires understanding not only its history but also how it adapts to modern challenges."
In summary, diving deep into the historical context of FIFO inventory management reveals a tapestry of practices woven over time, driven by necessity and innovation. As we venture further into the core principles, the adaptability of FIFO amidst the changing tides of commerce will be evident.
How FIFO Works in Practice
Understanding how FIFO operates in practice is crucial for businesses aiming to optimize their inventory management. At its core, FIFO ensures that the oldest stock is sold first. This is particularly vital in industries where products have a limited shelf life, like food and pharmaceuticals. Implementing FIFO doesn't just affect stock management; it impacts financial reporting, customer satisfaction, and even operational efficiency.
Operational Workflow in FIFO
The operational workflow in FIFO can be seen as a continuous circle of inventory movement. When new stock arrives, it's placed behind existing stock on the shelves. As orders go out, the oldest items are picked first. This simple yet effective flow helps in several ways:
- Reduced Waste: For businesses dealing with perishable goods, FIFO minimizes the chances of expiry.
- Inventory Accuracy: By keeping track of when items enter the inventory, businesses can better anticipate when stock needs to be rotated or replenished.
- Operational Simplicity: Staff members are trained to follow a straightforward process when picking items, which reduces confusion and improves efficiency often leading to quicker turnaround times.
"Proper rotation of stock in FIFO ensures minimal spoilage, making it a lifesaver for industries where shelf life is a concern."
Many businesses adopt specialized software to streamline this operational workflow, allowing for better tracking and quicker reordering of inventory.
Comparison with Other Inventory Systems
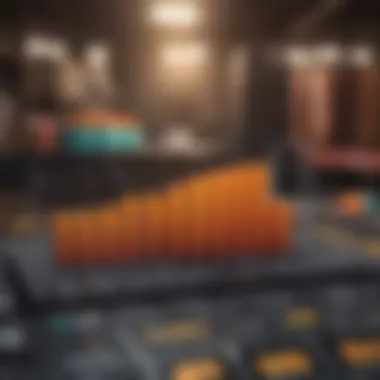
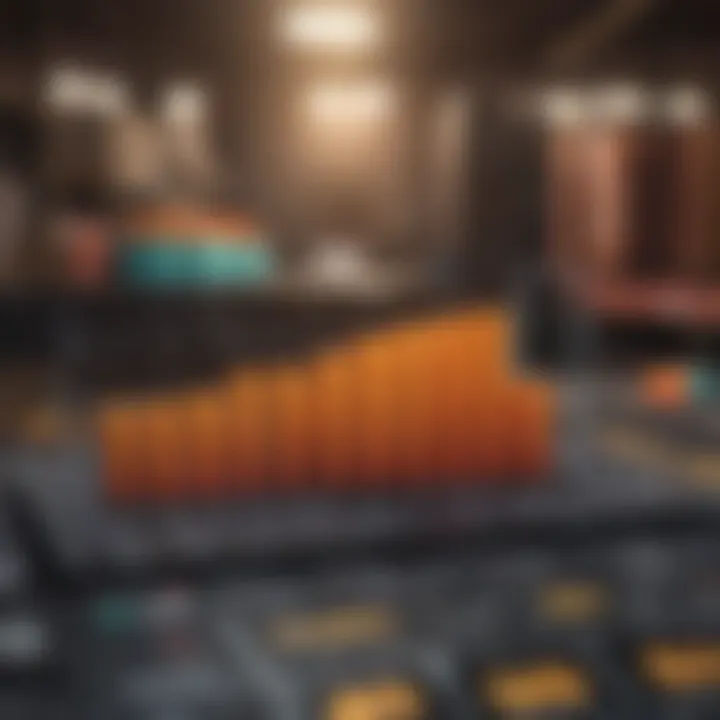
When we line FIFO up against other inventory management strategies, the contrasts become clear. Itās essential to comprehend not just FIFO, but also approaches like LIFO and Weighted Average Cost Method to figure out which best fits different business needs.
LIFO Overview
LIFO, or Last In First Out, operates on the opposite principle of FIFO. With LIFO, the most recently purchased items are sold first. This method can be beneficial in certain scenarios, primarily during periods of inflation. Here's why:
- Tax Benefits: Since LIFO often leads to higher cost of goods sold, this can reduce taxable income, thus benefiting cash flow in the short term.
- Valuation Impact: In a rising price environment, LIFO can provide a better estimation of the current costs of inventory on the balance sheet.
However, LIFO isn't without its drawbacks. It can lead to older inventory items remaining unsold for extended periods, which can be problematic for perishables. Additionally, LIFO may not be allowed under certain reporting frameworks, limiting its applicability in some contexts.
Weighted Average Cost Method
The Weighted Average Cost Method calculates the average cost of all inventory items, regardless of when they were purchased. This method has its own strong points:
- Simplicity: It simplifies bookkeeping since every item is valued identically.
- Stability: It smooths out price fluctuations over time, providing a more consistent picture of product costs.
Despite its advantages, the weighted average method may not offer the same level of accuracy when it comes to recognizing the actual flow of products. For industries where the timing of inventory turnover is essential, this method might not provide the insights needed for effective management.
In summary, while FIFO dominates particularly in industries where product freshness is critical, understanding its counterparts like LIFO and the Weighted Average Cost Method is key when evaluating the best fit for specific business models.
Benefits of FIFO Inventory Management
The practice of utilizing First In First Out (FIFO) inventory management brings several noteworthy advantages that can significantly enhance a business's operational efficiency and financial standing. Understanding these benefits forms a critical part of implementing effective inventory strategies. In this section, we delve into specific elements associated with FIFO, presenting a thorough analysis of the advantages it offers across various dimensions.
Enhanced Inventory Turnover
One of the most pronounced benefits of FIFO is the increased inventory turnover rate that businesses often experience. This system emphasizes the sale of older stock before newer arrivals, which helps maintain fresh inventory and minimizes the risk of obsolescence. By moving products in the order they are received, businesses can better align inventory levels with current demand, thus freeing up cash flow more quickly.
Additionally, a high turnover rate can signify efficient management practices to stakeholders, indicating that the business is actively selling its products rather than letting them sit on the shelves. This is a win-win situation:
- It allows for more timely replenishment of inventory.
- It reduces the carrying costs associated with unsold stock.
Moreover, businesses can leverage this turnover to reinvest profits into growth opportunities, ensuring they keep pace with market demands.
Improved Financial Reporting Accuracy
FIFO not only impacts inventory flow but also plays a crucial role in financial reporting. When businesses adopt FIFO, the older, often less expensive stock is accounted for first in the cost of goods sold (COGS) calculation. This aspect can lead to improved accuracy in reporting financial performance.
For instance, during periods of inflation, FIFO results in lower COGS than other methods like Last In First Out (LIFO). This lower cost can boost reported profits, presenting a more favorable view of profitability to investors. Thus, the potential benefits can include:
- Enhanced clarity in financial statements, enabling better decision-making for both management and shareholders.
- A more straightforward approach in audits, as older stock tends to require less record-keeping complexity.
However, it is essential to consider the implications of taxation, as higher reported profits may also lead to increased tax liabilities.
Minimization of Spoilage and Obsolescence
FIFO shines in scenarios where inventory is perishable or subject to rapid obsolescence. By prioritizing the sale of older items, businesses can significantly reduce losses related to spoilage or products becoming outdated. This is particularly relevant in industries such as groceries, pharmaceuticals, and fashion, where the shelf life of products is often limited.
The advantages can be summarized as follows:
- Reduced Losses: Businesses experience fewer write-offs due to unsold, outdated, or spoiled products, translating into better profitability.
- Customer Satisfaction: Fresher products are consistently available for consumers, which boosts customer trust and loyalty.
*"Maintaining the integrity of inventory by focusing on smaller, timely sell-throughs is a hallmark of a successfully managed operational structure."
Ultimately, the efficient management of inventory through FIFO conveys a commitment to both quality and responsibility. By minimizing spoilage and obsolescence, businesses can reinforce their brand reputation while optimizing operational efforts.
Challenges and Limitations of FIFO
First In First Out (FIFO) inventory management may seem like a straightforward method, but implementing it can come with its own set of challenges. Understanding the hurdles businesses may face while adopting FIFO is crucial. In this section, we will explore the complications that can arise in its implementation as well as the impact FIFO has on cash flow management.
Complications in Implementation
Implementing FIFO can often feel like trying to fit the square peg in a round hole, especially in businesses that haven't used structured inventory systems before. There are several factors that contribute to the complications in using this method.
- Physical Arrangement: The layout of a warehouse or storage space plays a significant role in FIFO's effectiveness. Older facilities might not be designed to allow easy access to the oldest inventory. This can lead to confusion among staff and potential errors in inventory rotation.
- Staff Training: Employees need to be adequately trained to follow FIFO protocols. A lack of understanding among staff regarding the best practices can result in older inventory not being sold first, which in turn could lead to spoilage or obsolescence.
- Inventory Tracking Systems: Not all inventory management software accommodates FIFO principles seamlessly. Customizing a system or integrating new technology can be a time-consuming and costly process. Moreover, if the software isnāt updated regularly, inaccuracies in tracking can arise, leading to further complications.
- Mixed Inventory Types: If a business carries multiple types of inventory, the implementation of FIFO becomes even trickier. For instance, products that come from different suppliers or batches might have varying expiration dates or characteristics, making it hard to determine which item is supposed to be first in line for sale. This creates a challenge in maintaining consistent FIFO flow.
"Navigating the maze of FIFO inventory management can often be a balancing act requiring both precision and ongoing vigilance."
Understanding these complications is essential for businesses to devise strategies to mitigate them.
Impact on Cash Flow
Cash flow is the lifeblood of a business, and adopting FIFO can have a significant impact on it. Here's how:
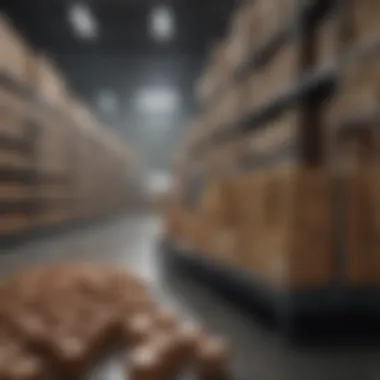
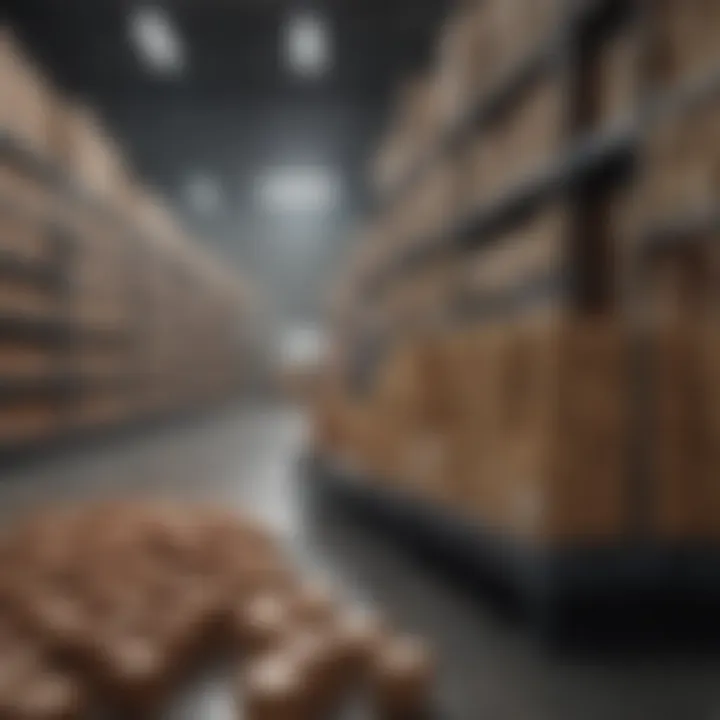
- Selling Price Variability: When using FIFO, businesses may sell older stock that could have been purchased at a lower price. As prices rise, the margin on these older products decreases, which can directly affect profit. This can create a situation where businesses have to adjust pricing dynamically to maintain their cash flow.
- Timing Issues: FIFO can lead businesses to sell inventory based on age rather than demand. If an item is old but in low demand, a company might find itself in a cash flow crunch, as resources are tied up in stock that wonāt move quickly.
- Increased Holding Costs: Older stock may require more storage time, which can result in increased holding costs. Whether itās the cost of physical storage space or the costs associated with managing goods that are not moving, businesses need to closely monitor these expenses to maintain healthy cash flow.
- Seasonal Inventory Fluctuations: For businesses selling seasonal goods, FIFO management can lead to cash flow challenges if they fail to anticipate demand. Older items might be pushed to the forefront, sidelining newer stock just as demand peaks for the latter.
This delicate balance underscores the need for strong management and forecasting capabilities when businesses decide to implement FIFO.
Industry Applications of FIFO
Diving into the various reasons why FIFO is an indispensable tool across industries reveals its significance in enhancing efficiency and accuracy in inventory management. Understanding how FIFO operates within different sectors not only highlights its adaptability but also uncovers the unique benefits that come with its use. Each industry brings its own requirements and challenges, which FIFO is equipped to address effectively.
Grocery and Perishable Goods
In the grocery sector, where products have limited shelf lives, FIFO becomes the backbone of inventory management. Retailers must move older products out first to prevent spoilage and minimize waste. Consider a grocery store's dairy section: milk and yogurt must be consumed before the newer stock to avoid loss. By prioritizing older products, businesses can reduce markdowns on unsold inventory and maintain customer satisfaction.
- Customer Trust: Using FIFO instills confidence among customers. A shopper needs assurance that they're purchasing fresh products. The feel of picking up a carton of milk with a recent expiration date can undoubtedly build brand loyalty.
- Waste Reduction: By adhering to FIFO, grocers effectively minimize wasted products. If older stock is sold first, the chances of products expiring before sale significantly decrease.
In sum, inventory that follows FIFO principles helps maintain quality standards, ultimately leading to a better shopping experience and higher profitability.
Manufacturing and Production Lines
Manufacturing industries often rely on FIFO to manage raw materials and finished goods. In a scenario where components are essential for assembly, such as in an automobile factory, using FIFO plays a crucial role in ensuring that materials are utilized in the order they are received. Here's how FIFO plays out in this sector:
- Process Efficiency: Older materials being used first can clear the floor of aged stock and ensure the production line keeps moving.
- Quality Control: Different batches of raw materials might exhibit variations in quality. Applying FIFO helps in identifying any discrepancies before they are integrated into the product.
Moreover, FIFO keeps manufacturing costs from spiraling. When businesses use newer stock, they benefit from recent acquisition prices rather than getting stuck with expensive older materials.
Pharmaceutical and Medical Supplies
In the pharmaceutical sector, FIFO takes on a life-or-death significance. With products that can be critical to health and recovery, managing inventory correctly is paramount. Medications, vaccines, and medical supplies have expiration dates that mandate strict adherence to FIFO practices. Hereās how FIFO is crucial in this field:
- Safety and Compliance: Using FIFO eliminates the risk of administering expired drugs, significantly buoying patient safety.
- Regulatory Standards: Regulatory agencies require pharmaceutical companies to demonstrate that they are using and distributing medicines in compliance with guidelines. FIFO provides a structured approach to inventory management that can be easily audited.
For example, a hospital pharmacy must first dispense older medications to ensure compliance and safety for patients. Failing to do so can lead not only to compromised patient safety but also to legal repercussions for the establishment.
"Effective inventory management isn't just about numbers; it's about reliability and trust."
Ultimately, these applications underscore how essential FIFO is to maintaining competitiveness and efficiency across the board.
The Role of Technology in FIFO Management
The role of technology in FIFO inventory management cannot be overstated. In a rapidly evolving marketplace, technology serves as a backbone, helping businesses streamline operations, minimize errors, and enhance decision-making. With increasing complexities in managing inventory, the integration of technology into FIFO processes elevates not only efficiency but also accuracy in tracking goods throughout their lifecycle. Businesses leveraging technology can improve their responsiveness to market dynamics and consumer demand, key elements in staying competitive.
Software Solutions and Tools
Various software solutions are available today that cater specifically to the FIFO method. These tools are designed to help organizations maintain accurate records of inventory and ensure that the stock is rotated properly. Commonly used software platforms include NetSuite, Fishbowl Inventory, and Zoho Inventory.
These tools generally offer features such as:
- Real-Time Tracking: They allow for the monitoring of stock levels in real-time, reducing the likelihood of running out of items or overstocking. This is crucial for effective FIFO management, especially in businesses with perishable goods.
- Reporting Capabilities: Tools provide analytical insights into inventory turnover rates and product performance, which often inform purchasing decisions, helping businesses to optimize their inventory levels.
- Integration with Other Systems: Most software solutions can seamlessly integrate with accounting, e-commerce, and supply chain management systems. This synergy not only enhances data validity but also ensures that all departments are on the same page.
By utilizing these software solutions, businesses can effectively address the challenges that come with FIFO inventory management, further ensuring that older stock is utilized first, thereby minimizing spoilage and costs.
Automation in Inventory Tracking
The move towards automation has revolutionized how inventory is tracked and managed within the FIFO framework. Automated inventory systems employ various technologies such as RFID scanners, barcode labels, and IoT devices to monitor stock movements accurately.
Some key benefits of automation include:
- Increased Speed and Efficiency: Automated systems drastically reduce the time spent on manual tracking, allowing organizations to focus on more strategic tasks rather than on tedious paperwork.
- Error Reduction: With machines handling repetitive tasks, the chances of human error are substantially diminished. This precision is vital when dealing with expiration dates or product life cycles, helping organizations stick to FIFO protocols reliably.
- Enhanced Data Accessibility: Automation offers accessible dashboards and reporting functionalities that allow stakeholders to view real-time inventory statistics. This instant access to data facilitates quicker decision-making and helps in maintaining the FIFO structure.
"Incorporating technology into FIFO isn't just about staying current; it's about providing a framework that allows businesses to thrive in an era of digital transformation."
Through careful implementation of technology in FIFO management, businesses are not only ensuring adherence to best practices but also fostering a culture of innovation and efficiency. Ensuring that inventory is managed correctly and responsibly can lead to significant cost savings and increased customer satisfaction.
Evaluating FIFO in Financial Reporting
Evaluating FIFO in financial reporting is a crucial component of understanding its overall impact on an organizationās economic health. This section sheds light on how FIFO influences profit and loss statements and tax obligations, which are essentially the backbone of any business's financial documentation. When companies evaluate their inventory using FIFO, they are positioning themselves to reflect accurate financial performance, providing stakeholders with valuable insights into profitability and resource allocation.
The method of FIFO assumes that the oldest inventory items are sold first. As a result, the value of the unsold inventory tends to be higher in times of rising prices, which can lead to a more favorable appearance in financial reports. Such evaluations are vital not only for internal management but also for investors and tax authorities. Understanding FIFO's principles in this regard enhances clarity and fosters better decision-making.
Impact on Profit and Loss Statements
The impact of FIFO on profit and loss statements (P&L) can be significant. By utilizing FIFO, businesses often report higher profits, especially during periods of inflation. Here's how it works:
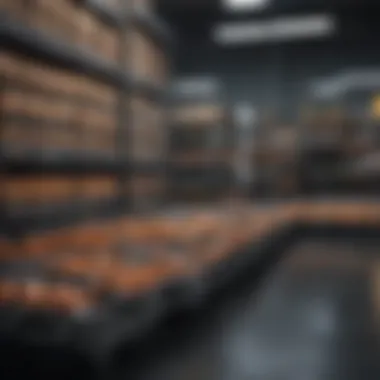
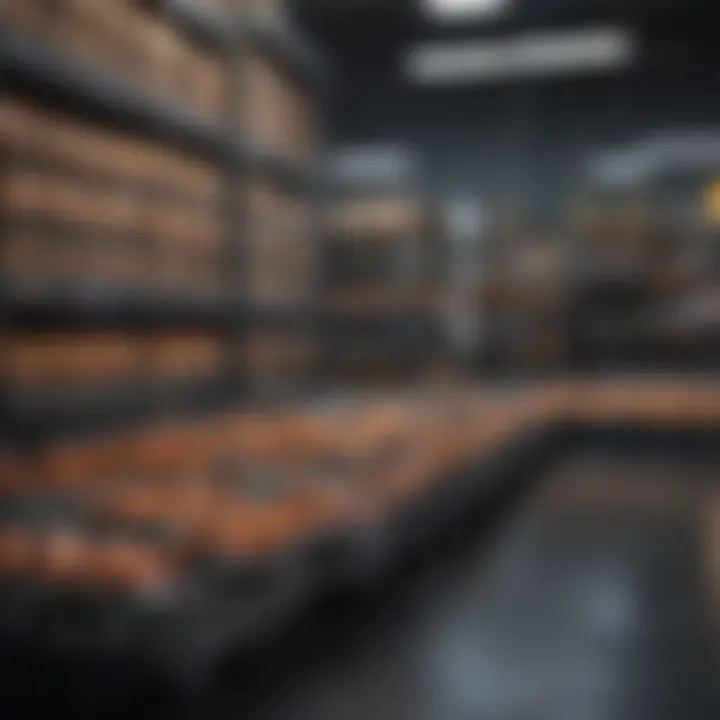
- Old Inventory Costs: When assessing product costs, FIFO matches older, cheaper inventory costs against current revenues. This typically results in lower cost of goods sold (COGS), thus increasing gross profit.
- Net Income Boost: With lower COGS, net income shows a positive trend on the P&L statement. Consequently, this amplifies performance metrics that stakeholders usually scrutinize.
- Tax Implications: Higher reported income might seem beneficial, yet it can lead to heavier tax liabilities. Companies must balance the benefits of improved profit margins with the ramifications of increased taxes.
In many businesses, the choice between FIFO and LIFO can effectively alter profit margins and tax burdens, leading to different financial strategies.
In times of fluctuating prices, this method reveals more about the companyās operational efficiency and ability to manage costs. Thus, stakeholders aim to view P&L statements with an understanding of FIFO's role in portraying financial health.
Adjustments for Tax Purposes
The relationship between FIFO and tax computations cannot be overlooked. For businesses, understanding these adjustments is fundamental for compliance and strategic planning. Here are some considerations:
- Taxable Income Calculation: As FIFO can lead to increased income on P&L statements, companies may face higher taxable income. This is directly tied to the increased profits resulting from lower COGS. Understanding accruing tax liabilities becomes essential.
- Inventory Valuation Adjustments: When a company chooses FIFO, they need to account for any changes in inventory valuation methods. Switching from one method to another can necessitate substantial documentation and adjustments.
- Long-Term Strategy: Overall, businesses need to evaluate their inventory methodologies in the context of their long-term financial strategies, which includes understanding tax obligations. Exploring options like LIFO for tax savings during inflationary periods could offer alternative pathways.
When businesses take the time to assess FIFO in terms of tax implications, they can better prepare for the financial responsibilities that lie ahead.
In summary, evaluating FIFO in financial reporting not only aids in reflecting profitability but also influences tax positions. Both the impacts on the profit and loss statements and necessary adjustments for tax purposes require careful analysis to navigate the financial landscape effectively.
Addressing Common Misconceptions About FIFO
In any discussion surrounding inventory management, clear misunderstandings can cause quite a few knots in practices and decision making. This section aims to unravel those misconceptions regarding First In First Out, or FIFO, to provide a clearer perspective. Proper comprehension of these issues is crucial, particularly for those investing time or resources into inventory strategies.
FIFO vs. LIFO Misunderstandings
When the conversation shifts to inventory methodologies, many people bring up the distinctions between FIFO and Last In First Out, or LIFO. One common error is believing that LIFO is inherently superior when it comes to managing inventory costs and profits. The truth is a bit more nuanced.
FIFO assumes that older inventory is sold first, which typically aligns with natural product flows, especially for perishables. This can be beneficial in sectors where products have expiration dates, like food or pharmaceuticals. Conversely, LIFO could lead to issues with spoiled goods when newer inventory is not cleared efficiently.
Moreover, a widespread concern is that FIFO will always result in higher reported profits during times of inflation because older, cheaper costs are matched against revenues. Although this might be true, itās essential to look at the whole picture. LIFO may reduce tax liability due to lower profit figures during inflationary phases, but it often creates challenges when pricing or reporting to stakeholders. The underlying point is that one system isnāt categorically better than the other; it depends entirely on the context and industry.
Perception of FIFO in Profit Margins
Another frequent misconception that needs to be tackled relates to the notion that FIFO guarantees higher profit margins across the board. While FIFO often leads to increased reported net income when inventory costs rise, it's not a guarantee of superior performance overall. This is crucial to understand when managing expectations.
The potential for increased profit due to FIFO's methodology means that many stakeholders misinterpret financial health based solely on profit margins without considering the cash flow implications.
In various circumstances, an inflated profit margin does not paint a complete picture. It may reflect well on paper, but the actual cash flowing into the business can be sluggish. Holding older inventory could lead to higher holding costs, which eats away at profits in another light, and substantially reduces flexibility when trying to capitalize on new market opportunities.
To summarize, while FIFO offers a structured framework for managing inventory that can optimize turnover and minimize spoilage, assuming it will always lead to higher profit margins is a misstep. Regardless of the chosen method, an inventory system demands ongoing scrutiny and adaptability, as economic contexts change, and business environments evolve.
Future Trends in Inventory Management
The realm of inventory management is undergoing a significant transformation, influenced predominantly by modern technology and changing consumer expectations. As businesses scramble to stay ahead of the curve, understanding the future trends in inventory management, particularly regarding FIFO, has never been more relevant. These future trends are crucial for enhancing efficiency, optimizing resource allocation, and ultimately boosting profitability.
Sustainability and Its Influence on FIFO Practices
In today's business landscape, sustainability is not merely an option; it's a necessity. As more consumers become environmentally conscious, businesses are reevaluating their operational practices, including inventory management systems like FIFO. The key drivers in this shift toward sustainability are legislative pressures, consumer demand for responsible sourcing, and the pursuit of cost reductions through waste minimization.
Adopting FIFO principles in conjunction with sustainable practices can lead to:
- Reduction in Spoilage: FIFO helps ensure that older products are sold first, reducing waste and spoilage, especially in industries dealing with perishable goods.
- Optimized Resource Utilization: Organizations can streamline logistics by efficiently managing stock levels, ensuring the use of resources is both economical and environmentally friendly.
- Enhanced brand reputation: Companies that prioritize sustainability often gain loyalty from consumers who value ethical practices.
Integrating sustainability into FIFO is not without its challenges. Companies must invest in training staff and implementing new technologies to monitor spoilage and inventory flow. However, the long-term benefits, including both financial and reputational gains, make these up-front investments worthwhile.
Data Analytics and Decision Making
The advent of big data and advanced analytics has opened new doors for inventory management, particularly for FIFO systems. The ability to analyze vast amounts of data allows businesses to make informed decisions that optimize inventory control and improve profitability.
Data analytics can enhance FIFO practices by:
- Demand Forecasting: Predicting consumer preferences and trends through data patterns enables businesses to adjust inventory levels accordingly, preventing overstocking or stockouts.
- Performance Metrics: Analyzing inventory turnover rates and sales velocity can provide insights into product performance, allowing companies to manage their FIFO processes more effectively.
- Cost Management: Data can spotlight inefficiencies in the supply chain, helping businesses identify areas for cost reduction without compromising on product availability.
By properly harnessing data analytics, companies can transform their FIFO inventory systems into powerful decision-making tools, enhancing operational efficiency.
As the future unfolds, it's clear that both sustainability and data analytics will play an integral role in the evolution of FIFO inventory management. Embracing these trends ensures that businesses remain competitive, adaptable, and responsible. In a world where consumer expectations are continuously evolving, those who stay ahead in these areas will likely reap the rewards.
Epilogue: The Importance of FIFO in Modern Business
In today's fast-paced market, the FIFO inventory management system stands as a critical pillar for various industries. By implementing FIFO, businesses can ensure that their inventory practices align with both financial prudence and operational efficiency. The method not only optimizes stock rotation but also plays an instrumental role in reducing waste, particularly in sectors dealing with perishable goods.
Recap of Key Points
Reviewing the discussions from earlier sections, several standout elements emerge:
- Optimal Inventory Turnover: FIFO allows for fresher stock to be sold first, significantly improving turnover rates. This is especially crucial in industries like food and beverage, where expiration dates dictate profitability.
- Accuracy in Financial Reporting: Utilizing FIFO can provide a more realistic view of profit margins during inflationary periods, as it reflects the true costs associated with older stock being sold first.
- Reduction of Spoilage: By ensuring that the oldest items are used first, FIFO minimizes the risk of spoilage and obsolescence, thereby preserving resources and enhancing sustainability efforts.
- Flexibility in Application: The versatility of FIFO allows it to be adapted seamlessly across various sectors, from grocery chains to pharmaceuticals, making it a widely accepted inventory management approach.
Final Thoughts on FIFO Implementation
As businesses navigate their operational strategies, adopting FIFO can usher in multiple advantages. However, it's vital to consider the specific context and needs of the organization. Implementation challenges can arise, particularly when shifting away from established processes. Therefore, training staff and revising systems to accommodate FIFO practices is paramount.
Moreover, in a realm increasingly driven by data, integrating technology into FIFO workflows can provide profound insights, further enhancing decision-making processes. Tools that facilitate real-time inventory tracking not only bolster accountability but also streamline operations.